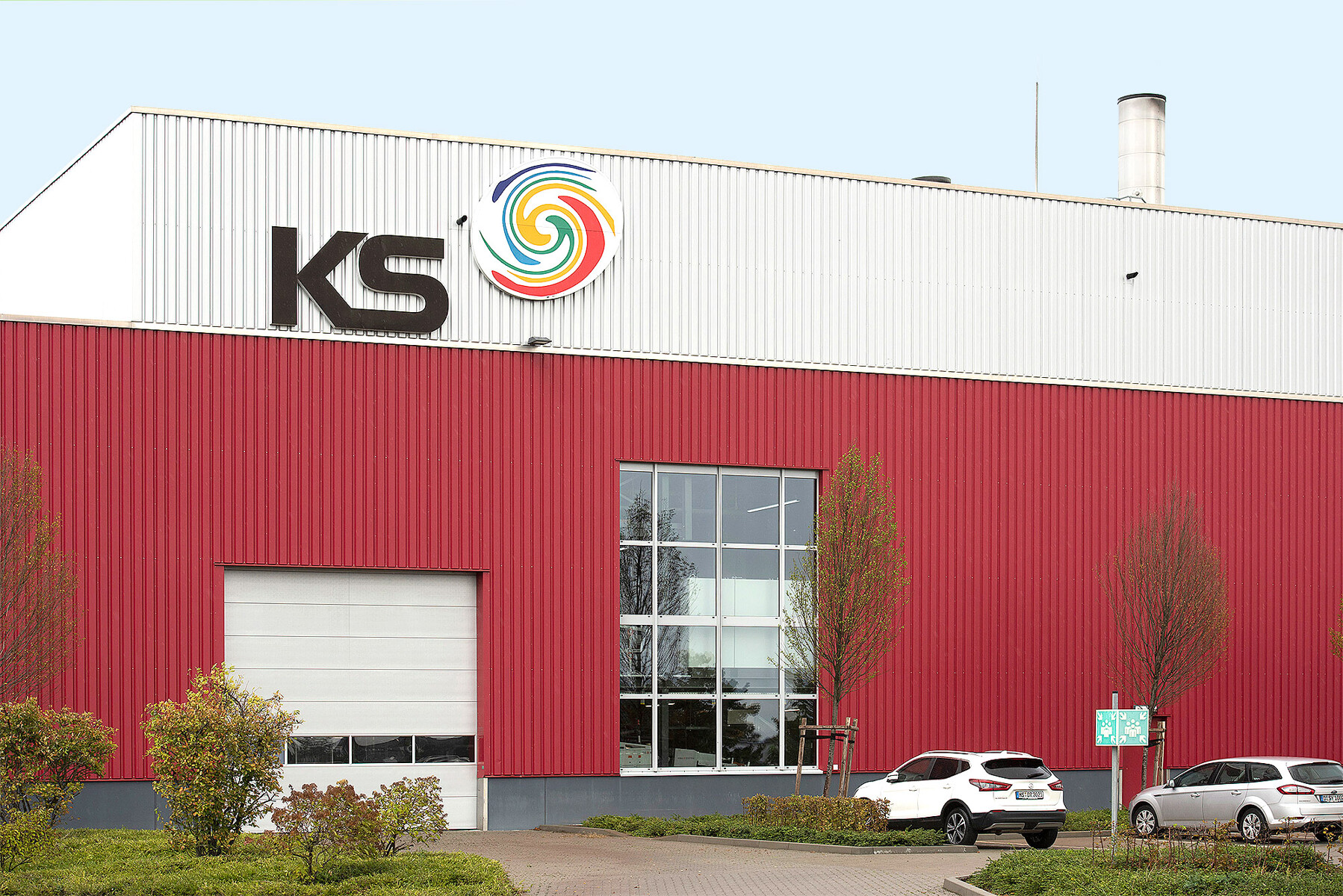
Welcome cooling for high-volume printing
In order to achieve sustainable improvements in its environmental performance, the web-fed offset printing company WKS Kraft Schlötes implements ISO 50001-compliant energy management. This involves continuously checking all processes for energy efficiency. These checks revealed that the water cooling system of the commercial printing press for brochure printing is an energy-intensive process. KSB won the contract to provide new pumps capable of achieving competitive energy and cost savings.
The Project: Pumps for a web-fed offset cooling water system
Radical changes in media consumption have exerted constant pressure on printing to become cheaper – while increasing in technical sophistication. If printing is to remain relevant in the age of digitalisation, it must be as cost-effective as possible. As web-fed offset printing presses become more powerful and complex, costs incurred during production-related downtime can increasingly spiral out of control. Against this challenging background, KSB was charged with finding an energy-efficient solution ensuring reliable operation.
The Customer: WKS Kraft Schlötes
Kraft Schlötes GmbH in Wassenberg, North Rhine-Westphalia, is a web-fed offset printing company that produces large volumes of brochures and newspaper supplements. It belongs to the WKS Group – which with 660 employees is one of Europe’s leading web-fed offset companies.
The web-fed offset printing press in operation
The challenge: Energy-efficient pumps and minimised downtime
In addition to achieving energy savings of almost 50%, KSB had another challenge to face: Web-fed offset printing plants of this size work in multi-shift operation around the clock, seven days a week. Under these conditions it was clear that modification of the cooling system had to minimise downtime for the printing press and ensure that production losses remained marginal.
The solution: Analysis, planning and implementation from one source
In collaboration with ENGIE, the specialist for heat dissipation systems in the printing industry, KSB began by evaluating data from the old pumps. The pump manufacturer then developed an energy cost calculation and determined which technology could be used to achieve the desired energy savings in the future. KSB was able to submit an offer for the new i.Cool cooling system from ENGIE which listed the total outlay for the new cooling system including all energy costs.
In terms of technology, the engineers opted for energy-optimised Etabloc pumps from KSB offering super premium efficiency to IE 4. Furthermore, the PumpDrive 2 variable speed system in combination with the PumpMeter pump monitoring unit ensured demand-driven operation and maximum energy savings.
An Etabloc pump with PumpDrive 2
The next stage saw specialists from KSB and ENGIE develop a strategy for replacing the cooling complex without creating long downtimes. It was agreed that large sections should be prefabricated and kept ready during ongoing operations before being installed in comparatively short breaks.
ENGIE’s employees were trained by KSB to commission the Etabloc pumps after delivery without KSB supervision. Once again, the kind of well thought-out product package which KSB offers its customers and project partners proved its worth: KSB’s pumps can be configured and commissioned after only a short training period.
After the new cooling system had been in operation for one year, ENGIE collaborated with WKS Kraft Schlötes to verify the consumption figures. The energy savings predicted in the previously prepared extrapolation were indeed confirmed and – at more than 50% – were even higher than the projected forecast. For WKS, ENGIE and KSB, this was confirmation that their cooperation had got everything right, all the way from analysis to planning and implementation.
Cooling unit with PumpDrive 2 variable speed systems and Etabloc pump; web-fed offset printing press in the background.
Figures I Data I Facts
Plant: Cooling water system for web-fed offset printing plant
End user: WKS Kraft Schlötes
Prodct data:
- 13 x Etabloc pumps with PumpDrive 2 and PumpMeter
Commissioning training of ENGIE employees by KSB
Products used
Etabloc
Ettrinns spiralhuspumpe med ytelser i henhold til EN 733, med utskiftbar akselhylse og spalteringer, med motormontert turtallsreguleringssystem. Med KSB SuPremE, en magnetfri synkronreluktansmotor (unntak: motordimensjoner 0,55 kW / 0,75 kW med 1500 min⁻¹ har permanentmagneter) i effektivitetsklasse IE4/IE5 etter IEC TS 60034-30-2:2016, for drift på turtallsreguleringssystem type KSB PumpDrive 2 eller KSB PumpDrive 2 Eco uten rotorposisjonsgiver. Festepunkter i henhold til EN 50347, dimensjoner i henhold til DIN V 42673 (07-2011). ATEX-utførelse tilgjengelig.
PumpDrive 2/PumpDrive 2 Eco
Selvkjølt frekvensomformer med modulær oppbygging som muliggjør en trinnløs turtallsendring av asynkrone og synkrone reluktansmotorer via analoge normsignaler, feltbuss eller betjeningsenhet. Takket være selvkjølingen til PumpDrive er det mulig med montering på motoren, på veggen samt i et koblingsskap. Regulering av opptil seks pumper uten ekstra regulator.
PumpMeter
Apparat for overvåking av driften til en pumpe. Det er en intelligent trykktransducer for pumper med et display som viser relevante måleverdier og driftsdata. Den registrer pumpens belastningsgrad for eventuelt å signalisere et optimeringspotensial for økning av energieffektivitet og tilgjengelighet. Enheten består av to trykksensorer og en visningsenhet. PumpMeter er komplett montert på fabrikken og er gjort parametrisk for den respektive pumpen. Den kobles til via en M12-kontakt og er umiddelbart driftsklar.